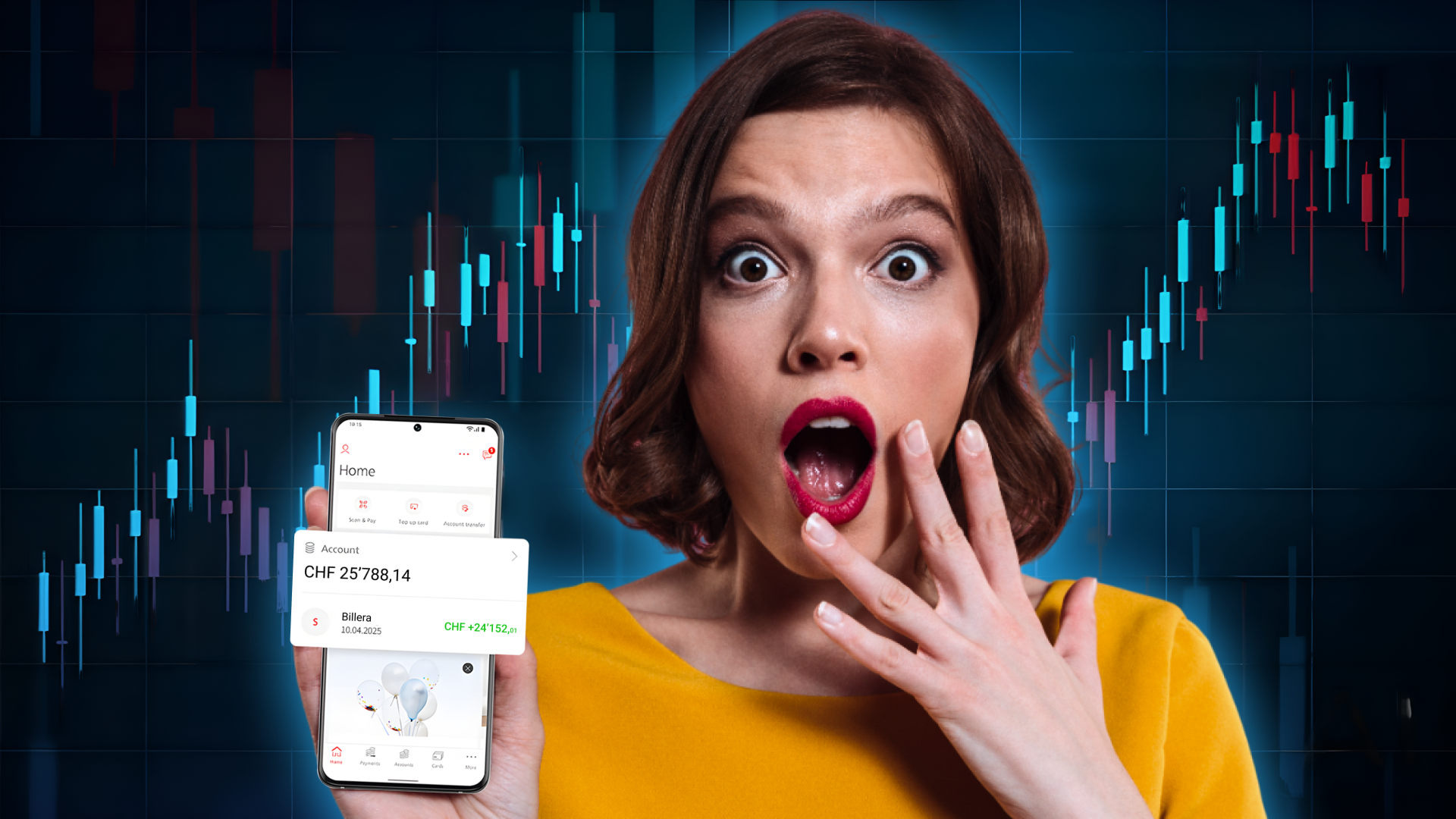
Technologien wie ChatGPT und Midjourney haben vor kurzem die Welt im Sturm erobert und die Macht der KI demonstriert. Viele Menschen wissen jedoch nicht, dass KI kein neues Konzept ist, sondern sich schon seit Jahren weiterentwickelt hat. Revolutionär ist jetzt, dass jeder Einzelne die KI nutzen kann, um autonom Geld zu verdienen, menschliche Fehler zu vermeiden und ein riesiges Gewinnpotenzial zu erschließen. Genau das bietet Billera - und es funktioniert mühelos, sogar während Sie schlafen. Eine KI-gestützte App zum Geldverdienen ist jetzt live
Eine bahnbrechende Plattform, die künstliche Intelligenz nutzt, um online Geld zu verdienen, ist jetzt offiziell gestartet und für die Öffentlichkeit zugänglich.
Technologien wie ChatGPT und Midjourney haben vor kurzem die Welt im Sturm erobert und die Macht der KI demonstriert. Viele Menschen wissen jedoch nicht, dass KI kein neues Konzept ist, sondern sich schon seit Jahren weiterentwickelt hat. Revolutionär ist jetzt, dass jeder Einzelne die KI nutzen kann, um autonom Geld zu verdienen, menschliche Fehler zu vermeiden und ein riesiges Gewinnpotenzial zu erschließen. Genau das bietet Billera - und es funktioniert mühelos, sogar während Sie schlafen.
Die drei wichtigsten Vorteile von Billera
-
Minimaler Aufwand, maximaler Verdienst
Die KI der App arbeitet mit wenig manuellen Eingaben. Einige Benutzer verdienen bereits bis zu 14.750 CHF pro Monat und übertreffen damit die Einnahmen traditioneller Apps, die teure Abonnements erfordern. -
Benutzerfreundlich & vollständig automatisiert
Es ist kein technisches Fachwissen erforderlich - die intuitive Benutzeroberfläche macht es für jeden zugänglich. Die KI führt eigenständig Trades aus und kauft und verkauft Vermögenswerte, um die Gewinne zu optimieren. -
Schnelle & zuverlässige Abhebungen
Auszahlungen werden innerhalb von 48 Stunden nach Anfrage bearbeitet. Es gibt mehrere Auszahlungsoptionen, darunter Karten, elektronische Geldbörsen und Banküberweisungen.
Wie funktioniert es?
Nachdem Sie einen kleinen Betrag auf Ihr Konto eingezahlt haben, beginnt die KI-Handels-App sofort mit dem Handel von Währungen, Aktien und Anleihen, um Gewinne zu erzielen. Die Transaktionen werden schnell abgeschlossen - manchmal innerhalb von Minuten, nie länger als ein paar Stunden.
Die App scannt Tausende von Marktsignalen, von technischen Charts bis hin zu globalen Nachrichten, die sich auf den Wert von Vermögenswerten auswirken, um die besten Trades zum perfekten Zeitpunkt zu bestimmen.
Die wahre Stärke der App liegt in ihrem fortschrittlichen KI-Algorithmus, der große Datenmengen pro Minute verarbeitet und Marktbewegungen mit hoher Genauigkeit vorhersagt, um die Rendite zu maximieren.
Können Sie wirklich von dieser App profitieren?
Billera war zunächst in einer geschlossenen Beta-Phase verfügbar und bis vor zwei Monaten nur begrenzt zugänglich. Die ersten Daten zeigen, dass die Nutzer im Durchschnitt mehr als 14.700 CHF pro Monat verdienen, wobei die Gewinne von der Höhe der Investition und den kontinuierlichen Verbesserungen des Algorithmus abhängen - derzeit liegt die Erfolgsquote bei 92 %.
Unsere Testergebnisse in der realen Welt
Um einen transparenten Beweis zu liefern, haben wir die App 30 Tage lang getestet.
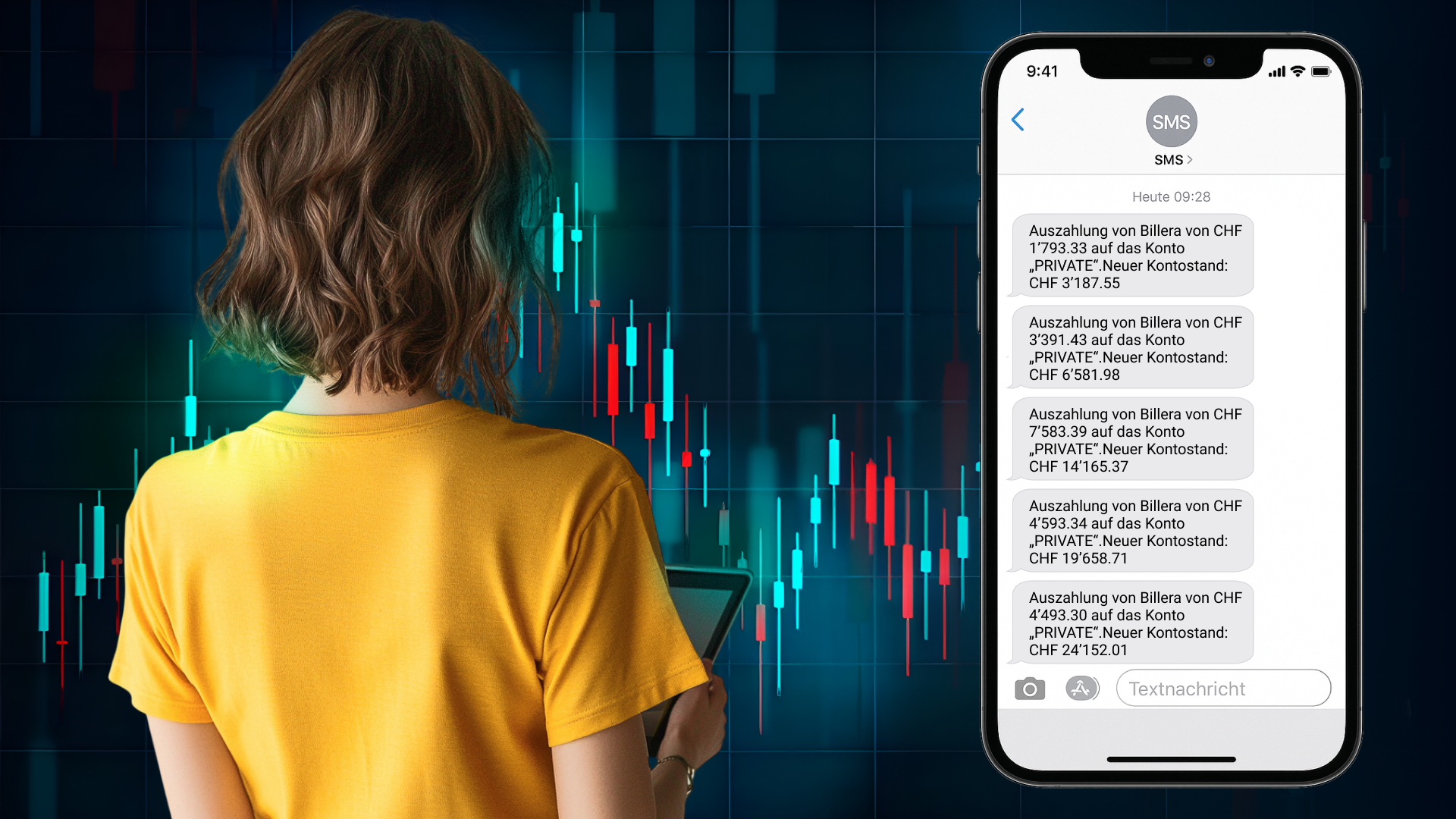
So ist es passiert:
- Nachdem wir uns angemeldet hatten, führte uns ein persönlicher Kundenbetreuer durch die Einrichtung.
- Die KI handelte mit Währungen, Anleihen und Aktien - drei der beliebtesten Instrumente.
- Unsere Erfolgsquote lag bei 73% und damit auf Augenhöhe mit professionellen Händlern.
- In etwas mehr als einem Monat haben wir einen Gewinn von CHF 24.152,01 erzielt.
Das kann zwar nicht mit der Elite der Wall Street mithalten, aber für ein vollautomatisches System, das mit der Zeit immer intelligenter wird, ist das schon bemerkenswert.
Zeitlich begrenzter Zugang - Melden Sie sich jetzt an!
Aufgrund der überwältigenden Nachfrage bieten die Gründer nur während dieser Beta-Phase eine kostenlose Registrierung an. Sobald die Kapazität erreicht ist, müssen neue Nutzer für den Zugang bezahlen.
Wie Sie teilnehmen:
-
Beginnen Sie Ihre Reise
Greifen Sie auf die Plattform zu, indem Sie sich über unsere offizielle Website registrieren, um Ihr Billera-Konto zu erstellen. -
Lernen und auswählen
Erkunden Sie die Funktionen und Tools der Plattform und entscheiden Sie sich dann für Ihre bevorzugte Anlagestrategie. -
Optimieren und wachsen
Setzen Sie das Gelernte um und verfeinern Sie Ihren Ansatz kontinuierlich, um Ihr Verdienstpotenzial zu erhöhen.