In the 1950s, China began to use induction heat treatment technology and equipment in the automotive industry. Since the 1980s, especially with the rapid development of the automobile industry in the past 20 years, the types and varieties of induction heat treatment parts in China have been increasing. Taking commercial vehicles as an example, the number of induction hardened parts reaches more than 100, accounting for about 70% of the total number of heat-treated parts. The level of induction heat treatment technology in China is close to or reaches the international advanced level.
1. Induction heat treatment process
The induction heating process is the main embodiment of the level of induction heating technology. The advanced induction heating technology can effectively utilize the characteristics of induction heating to achieve efficient and energy-saving local heat treatment. At present, there are many materials for induction hardening of automobile parts, including 35 steel, 45 steel, 40Cr, 55MnVS, 40MnB, 42CrMo, ZG45, ductile iron and alloy cast iron. The heating quenching method and application are numerous, for example, the transverse magnetic field of the pin shaft and the cam shaft is statically quenched once; the transverse magnetic field of the damper rod, the torsion bar and the shifting differential shaft is continuously heated and quenched; the starter shaft and the air compressor shaft are horizontally Multi-stage continuous heating and quenching of magnetic field; one-time vertical magnetic field and one-time heating and quenching; one-time and continuous heating and quenching of inner flange of inner flange and inner cavity of bell-shaped shell; induction and hardening of steering rack induction contact; stepped shaft knuckle and after car Rotary heating and quenching of the hub axle; primary and continuous heating quenching of the plane-type leaf spring lateral limiting plate; primary and continuous heating quenching of the thin-walled sliding shaft fork and the front hub; one-time heating and quenching of the complex-shaped bell-shaped shell variable-section shaft Wait.
In the aspect of automobile gear induction heat treatment, based on the consideration of production efficiency and the characteristics of automobile gear parts, China mainly adopts the integral induction heating quenching process, namely single frequency heating quenching and double frequency heating quenching. The most common use of automotive gear induction hardening is the engine flywheel ring gear. Dongfeng Motor Corporation has already achieved induction hardening in some transmission gears, and replaced the high-priced carburized gear steel with cheap medium-carbon alloy steel, which has achieved good economic benefits.
Now, the most advanced and representative German Eldec SDF synchronous dual-frequency induction heating equipment and process is a surface heat treatment equipment and process with energy saving, consumption reduction and green production, and can obtain minimum heat treatment deformation and uniform along the tooth profile. The hardened layer is distributed to achieve the best heat treatment quality. It has been widely used in automotive (such as automotive CV joints, drive shafts, steering gear units, spiral bevel gears and driven planetary gears) and heat treatment of complex surface workpieces such as gears in the aerospace industry, in Germany, BMW and Volkswagen. The US Boeing Aircraft Manufacturing Company has also been applied. This process and equipment will become one of the trends of induction heating and quenching. Figure 6 shows the modular induction heating and quenching equipment of eldec.
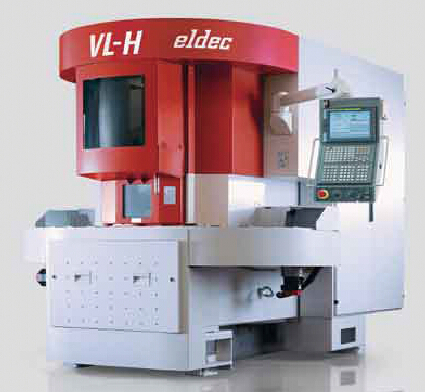
Figure 6 eldec modular induction heating and quenching equipment
2. Induction heat treatment equipment
In order to adapt to the mass production of various varieties, in the production and application of auto parts, the types of induction hardening machines introduced and developed in China are gradually developed from traditional special equipment to general-purpose equipment with high degree of flexibility and special quenching automatic production lines, and CNC control technology is adopted, and control systems such as FANUC and SIEMENS are applied. FAW and Dongfeng Motor Corporation have successfully developed a number of large-scale induction hardening complete sets of equipment (production lines), reaching the international advanced level.
The horizontal CNC quenching machine developed by FAW Technology Center is driven by the main drive AC servo motor. The moving speed is stable and uniform, the positioning is accurate, and the repeating precision is high. The part rotation adopts the variable frequency speed control system, which can adapt to various process requirements; The numerical control technology inducts and quenches the parts with different performance requirements, and even realizes multi-stage variable power shifting on the same part, which is easy to program and operability.
Dongfeng Motor Corporation research and development of fully automatic crankshaft quenching equipment, using power distribution, thin quenching transformer, independent suspension, buffer feed, rotary quasi-stop and other new technologies, with equipment monitoring, fault diagnosis, parameter recording and parts repair, etc. Features. In addition, an analog control panel is designed, and the operator can control the machine action through the mouse or keyboard. The device hangs more than three sets of thin transformer-inductor units at the same time as needed, and does not need to replace the sensor during operation. As long as the crankshaft is placed on the machine's material level during the work, the equipment can automatically complete the quenching process without manual operation. Figure 7 shows a crankshaft quenching machine.
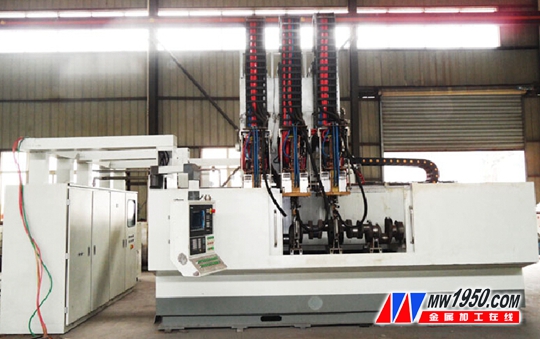
Figure 7 Crankshaft quenching machine
At present, the high-power power supply has been industrialized in China, the quality is stable, the price is only 1/3~1/2 of the imported power supply, and the domestic quenching SCR power supply can achieve 2000kW; the new IGBT power supply has a wide operating frequency range and load adaptability. Strong, high electrical efficiency, process adjustment is very convenient, the frequency range covers 1 ~ 100kHz, the power reaches 1000kW, can replace the import, and has achieved partial exports.
In general, there are still some gaps in the level of induction heat treatment technology in China compared with advanced countries, such as the application of numerical control technology, computer technology and precision mechanical transmission technology in quenching machine tools; high quality and high reliability in power supply. Development of power components; manufacturing technology for precision sensors. With the improvement of the automation control level of the induction heat treatment production line and the high reliability requirements of the power supply, it is necessary to strengthen the development of the heating process complete device. At the same time, the induction heating system is developing in the direction of intelligent control. The induction heating power system with control functions such as computer intelligent interface, remote control and automatic fault diagnosis is becoming the development goal of the next generation.
Chongqing Xingjida Import and Export Trade Co., Ltd. , https://www.xjdvalve.com